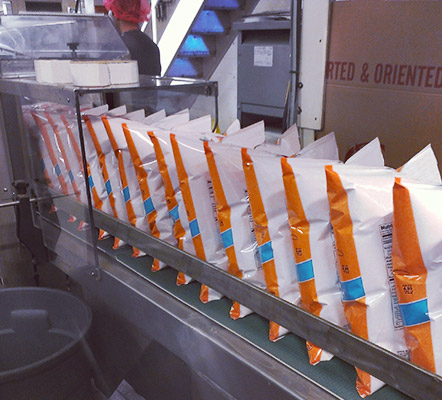
Benefits of Ultrasonic Sealing
At EWI UltraThinSeal™, we’ve tested, tuned up and proven our patented technology to offer undeniable advantages across the packaging industry. The benefits are definite for many businesses:
- Consumer packaged goods companies (CPGs)
- Original equipment manufacturers (OEMs)
- Retail businesses
- Film and resin suppliers
- Film converters
Expect the Best from Our Technology
Economical & Efficient
- Reduces material by 8-12% without reducing the package size
- Reduces energy consumption
- Improves seal quality, leading to a 40% reduction in scrap rate
- Extends shelf life by up to 4 weeks, leading to new product options
- Is faster than heat sealing in many applications
- Can be used to significantly shrink package size, leading to higher-density cartons and more shelf space
Sustainable & Safe
- Is compatible with sanitation processes (wash-downs)
- Reduces landfill waste by 8% on average
- Eliminates adhesives
- Is compatible with recyclable materials, biodegradable materials and PLA
- Doesn’t heat up surrounding film – no employee burns, melted product or ruined film
Easy to Implement
- Is easily retrofitted on existing machines
- Is simply integrated into new machines
UltraThinSeal Sealing vs. Traditional Heat Sealing
A diverse range of businesses benefit when they, or their vendors, use ultrasonic technology instead of thermal sealing ‒ and so do their consumers. See the differences; think of the possibilities.
Size:
While thermal seals are, on average, 13 millimeters (a half inch) wide at the top of a package, our new way of sealing can produce bags with seals that measure 1 to 2 millimeters wide. The bag itself can be made smaller too, as the tiny, quality seal allows for smaller headspace requirements, with no worries about excessive oxygen transmission or the product getting caught in a wider seal. With the seal and bag size reduced, material savings can approach 25 percent.
Material Options:
Our ultrasonic sealing system can be used on a broad range of package sizes and film types, such as PLA, as long as the material has a thermoplastic component. We’ve proven its effectiveness on biopolymers and biodegradable polymers as well. Heat sealing, on the other hand, can only be used on a few types of films with specific width and thickness. Because ultrasonic methods open up more possibilities for materials, less-expensive alternatives can be explored.
Quality:
Our ultrasonic sealing system produces far fewer “leaker” packages than traditional sealing methods, which extends the shelf life of the product inside. This is possible in part because the technology can seal properly even if a minor contaminant is present. In fact, a client reduced their leaker rate from 1.5% to .87% percent after switching to our system (from thermal sealing); when you’re sealing millions of packages annually, as they are, this is quite a significant improvement. Finally, since there’s no sealant involved, there’s no risk of damaging the still-hot sealant – or wasting money and time on it.
Possibilities:
Taking advantage of diverse film options creates packaging that looks as revolutionary as the technology that sealed it. Longer shelf life enables shipments into farther markets, less waste and even new product options. Additionally, the lack of residual heat during ultrasonic sealing means you can package, with complete confidence, products and films that are prone to melting.
End-User Experience :
Five million packages have been brought to market with UltraThinSeal technology, and there have been no complaints from consumers about package quality, stale or broken product, or any other issue. A client reported that, with thermal sealing equipment, they used to receive about eight complaint calls per million packages, but this was resolved when they implemented our system.
Want to Know More?
Check out our FAQ page to get answers for the most common questions we hear.
Visit our Technology page to see just how ultrasonic package sealing works in new and existing equipment.
To talk one-on-one with one of our experts about your specific needs or ideas, call us at 972-489-7192 or contact us online.